
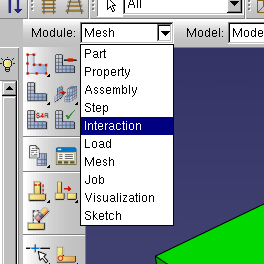
For more information about the Getting Started plug-ins, see “Running the Getting Started with Abaqus examples, ” Section 82.1 of the Abaqus/CAE User's Guide. To run the script from Abaqus/CAE, select Plug-ins Abaqus Getting Started highlight Flow through a bent tube and click Run. If you encounter difficulties following the instructions given below or if you wish to check your work, you can run the plug-in script for this example, which is available in the Abaqus/CAE Plug-in toolset. Abaqus provides scripts that replicate the complete analysis model for this problem. This tutorial discusses how to use Abaqus/CAE to create the entire model for this simulation. In the Edit Model Attributes dialog box, enter fluid-cfd as the name and select CFD as the type. After that analysis you will perform a fluid-structure interaction analysis in which the tube is considered deformable. You will first perform a pure flow analysis in which the tube is assumed rigid. The excellent correlation of the internal geometry and the elastic properties underlines the framework’s potential for future damage modelling.Start Abaqus/CAE (if you are not already running it). The framework was validated by detailed comparison with experimental results for three braid architectures. A novel meshing methodology incorporates branching cohesive yarn-to-yarn and yarn-to matrix interfaces for modelling delamination. For mechanical simulation, a matrix pocket mesh is created from a reconstruction of the deformed textile.
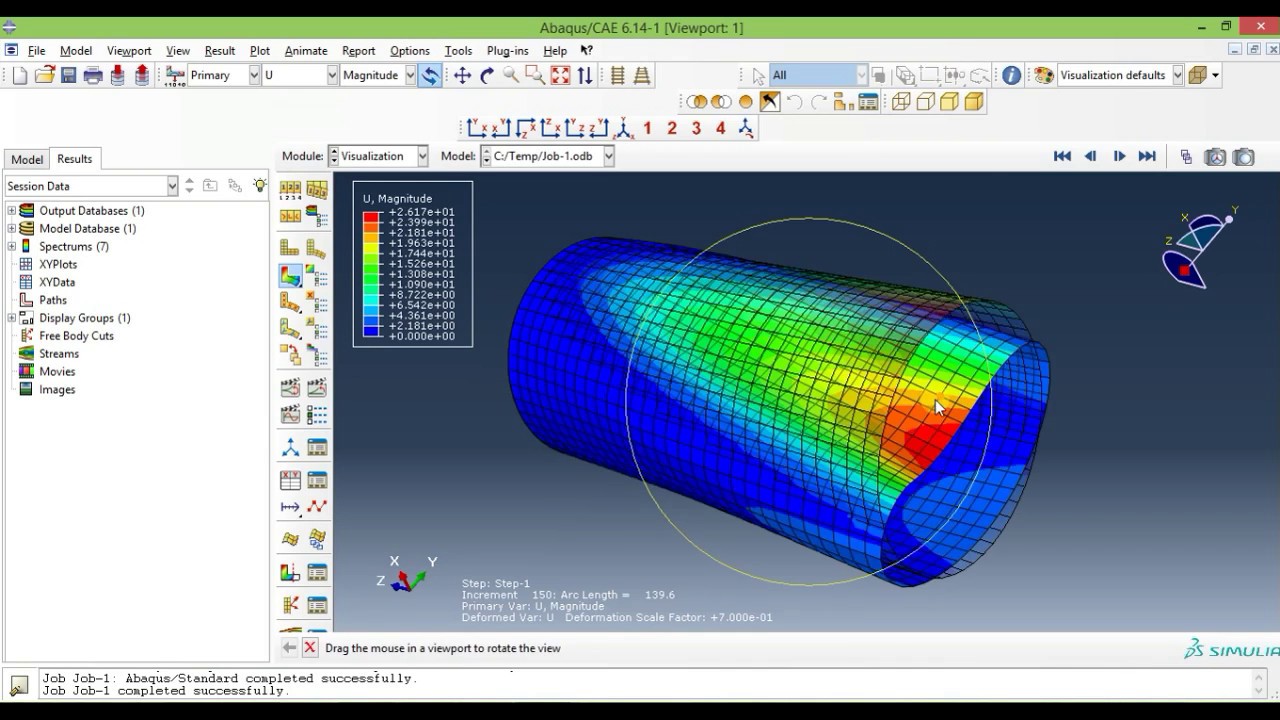
A compaction simulation of a single textile layer is performed to the desired target fibre volume fraction while implicitly considering multiple plies in different nesting configurations through periodic boundary conditions. Local volumetric interpenetrations are removed from a nominal geometry in a fictitious thermal simulation step. Edge seed - Uniform - Biased - By size - By number Structured Meshing 1-D 2-D regions 3-D solid. Unit cells with a realistic internal geometry are generated within an automated simulation work-flow. Global seed size ABAQUS/CAE 6.14 DATA SHEET. In this paper, we propose a novel simulation framework for accurately predicting the mechanical response of highly compacted triaxial braided composites using meso-scale finite element models.
